Alt akışta çok fazla su ve taşmada çok fazla katı madde mi var? Tekrarlanan yoğunluk ölçümlerini ve insan hatalarını ortadan kaldırarak yoğunlaştırıcının çalışmasını optimize etmeyi mi düşünüyorsunuz? Mineral işleme sektöründe birçok son kullanıcı, su tasarrufu yapmak ve işleme için değerli malzeme toplamak konusunda aynı sorunlarla karşılaşıyor. Gerçek zamanlı yoğunluk ölçer, bu hedeflere ulaşmada verimli bir şekilde çalışır.
Aşağıdaki makale, yoğunlaştırıcı tanklarının farklı noktalarında yoğunluk kontrolünün amaçlarını ve faydalarını açıklamaya odaklanmaktadır. Yoğunlaştırma sürecine kısa bir girişle başlayıp, ayırma sürecinde yoğunluk ölçümünün beş nedenini ele alacağız.
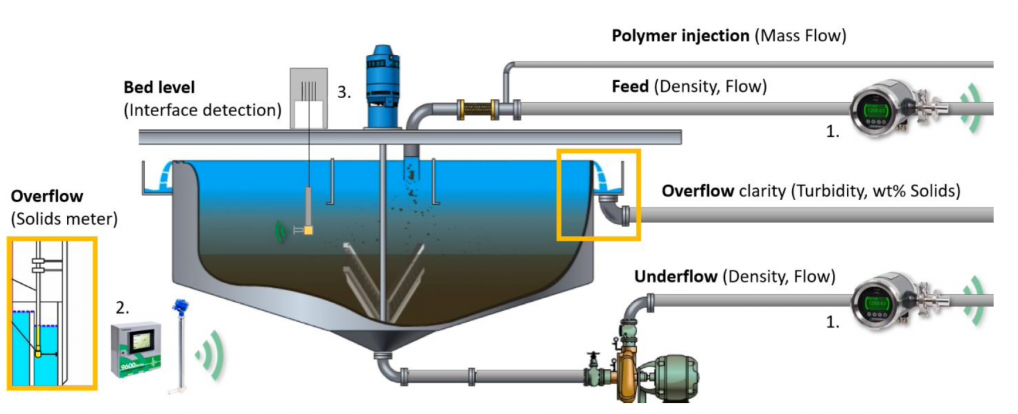
Kalınlaştırmanın İşlevi Nedir?
Yoğunlaştırma işlemi, katı-sıvı karışımının tipik olarak yoğun bir alt akış ve berrak bir taşma olmak üzere iki katmana ayrılmasını içerir. İlki katı parçacıklardan oluşurken, ikincisi mümkün olduğunca safsızlıkları dışarıda tutar. Ayırma işlemi yerçekiminin bir sonucudur. Farklı boyut ve yoğunluktaki tüm parçacıklar tank boyunca farklı katmanlar oluşturur.
Yoğunlaştırma işlemleri, mineral işleme tesislerinde, konsantre ve atıkların ayrılması amacıyla sedimantasyon tankında gerçekleşir.
Kalınlaştırmada Gerekli Ölçüm Noktaları
Çevrimiçi sıvı yoğunluk ölçerlerYoğunlaştırıcıların çalışmasını optimize etmek için gereklidir. Örneğin, kurulum noktaları arasında yoğunlaştırıcı tankının besleme, alt akış, taşma ve iç kısımları bulunur. Yukarıdaki koşullarda, bu sensörlerbulamaç yoğunluk ölçerveyaçamur yoğunluk ölçerAyrıca tahriklerin, pompaların otomatik kontrolünün iyileştirilmesinde ve flokülantların etkili bir şekilde dozlanmasında da yardımcı olurlar.
Yoğunluk Ölçümünün Nedenleri
Yoğunluk ölçümünün nedenleri kişiden kişiye değişebilir. Aşağıdaki beş koşul, endüstriyel optimizasyon için yoğunluk izlemenin önemini vurgulamaktadır.
1 Numaralı Su Geri Kazanımı
Su, madencilik ve mineral endüstrisinde en önemli varlıklardan biri olarak kabul edilir. Bu nedenle, suyun geri kazanımı veya tekrar kullanımı, yoğunlaştırma maliyetini büyük ölçüde azaltır. Alt akış yoğunluğunda %1-2'lik küçük bir artış, işletme tesisleri için büyük miktarda suya ihtiyaç duyulacağı anlamına gelir. Yoğunluğun artması, barajlara çok fazla sıvı pompalanması durumunda çökebilecek olan atık barajlarının sağlamlığını garanti altına almada etkili bir şekilde çalışır.
2 Numaralı Maden Geri Kazanımı
Konsantre yoğunlaştırıcılarda besleme genellikle flotasyon devresinden gelir. Flotasyon, parçacıkların yerçekimi yoluyla ayrılmasını içerir. Başka bir deyişle, üzerinde hava kabarcıkları bulunanlar yüzeye çıkıp uzaklaştırılırken, diğerleri sıvı fazda kalır. Bu işlem ürün yoğunlaştırıcısında gerçekleştiğinde, köpük katıları taşma kanalına taşıyabilir.
Bu katılar değerlidir ve geri kazanılmazlarsa, konsantre metalin genel geri kazanım oranını düşürebilirler. Ayrıca, taşmadaki katılar daha yüksek reaktif maliyetlerine, pompa ve vanalarda hasara ve katılar biriktiğinde proses suyu tanklarının temizlenmesi gibi bakım masraflarının artmasına neden olabilir.
Taşmada kaybolan katıların yaklaşık %90'ı, sürecin sonraki aşamalarında (örneğin tanklarda ve barajlarda) geri kazanılır. Ancak, önemli bir ekonomik değere sahip olan kalan %10'luk kısım kalıcı olarak kaybolur. Bu nedenle, taşmada oluşan katı kaybını azaltmak öncelikli olmalıdır. Proses kontrol teknolojilerine yatırım yapmak, geri kazanım oranlarını artırabilir ve yatırımın hızlı bir şekilde geri dönüşünü sağlayabilir.
Lonnmeter'ın kullanımıyoğunluk ölçerlerVeakış ölçerlerAlt akıştaki katıların tespiti, yoğunlaştırıcı performansının daha iyi izlenmesini sağlar. Yoğunluk veya katı madde ölçüm cihazlarıyla taşma akışındaki katıların gerçek zamanlı tespiti de mümkündür. Cihazların 4-20 mA sinyalleri, doğrudan proses optimizasyonu için kontrol sistemine entegre edilebilir.
3 Verimli Flokülant Kullanımı
Flokülantlar, sıvılardaki partiküllerin topaklanmasını kolaylaştıran kimyasallar olan sedimantasyon verimliliğini artırmada etkilidir. Flokülantların dozajlanması, reaktif maliyet kontrolünü ve işletme verimliliğini dikkate alır. Yoğunluk ölçer, koyulaştırıcı beslemesi için hassas ve güvenilir yoğunluk kontrolü sağlar. Amaç, besleme bulamacında ağırlıkça mümkün olan en yüksek katı yüzdesini elde ederken serbest partikül çökelmesini sağlamaktır. Besleme bulamacının yoğunluğu hedefi aşarsa, ilave proses sıvısı eklenmeli ve yeterli besleme kuyusu karışımını sağlamak için daha fazla karıştırma enerjisi gerekebilir.
Besleme bulamacının hat içi yoğunluk ölçer kullanılarak gerçek zamanlı yoğunluk ölçümü, proses kontrolü açısından hayati önem taşır. Bu, verimli flokülant kullanımını sağlar ve karıştırma sürecini optimize ederek koyulaştırıcının hedef aralığında çalışmasını sağlar.
4 Flokülasyon Sorunlarının Anında Tespiti
Operatörler, yoğunlaştırıcılarda sabit koşulları korumaya çalışırlar; minimum katı madde içeren berrak bir taşma ve minimum sıvı içeren yoğun bir alt akış elde ederler. Ancak, proses koşulları zamanla değişebilir ve bu da potansiyel olarak zayıf çökelmeye, alt akış yoğunluğunun azalmasına ve taşmada daha yüksek katı madde içeriğine yol açabilir. Bu sorunlar, flokülasyon sorunlarından, tanktaki hava veya köpükten veya beslemedeki aşırı yüksek katı madde konsantrasyonundan kaynaklanabilir.
Enstrümantasyon ve otomasyon, operatörlerin bu tür sorunları gerçek zamanlı olarak tespit ederek kontrolü sürdürmelerine yardımcı olabilir. Hat içi ölçümlerin yanı sıra, ultrasonik yatak seviyesi probları gibi tank tabanlı enstrümantasyonlar kritik bilgiler sağlayabilir. Bu "dalgıç" problar tank içinde yukarı ve aşağı hareket ederek çamur seviyelerini, çökme bölgelerini ve taşma berraklığını belirler. Yatak seviyesi ölçümleri, özellikle flokülasyon kontrol stratejileri için kullanışlıdır ve tutarlı performans sağlar.
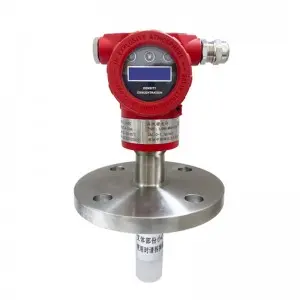
Bulamaç Yoğunluk Ölçer (SDM)
Bulamaç Yoğunluk Ölçer (SDM), geleneksel nükleer yoğunluk ölçerlere çevre dostu bir alternatiftir. Dünya çapında yüzlerce kurulumuyla hızla popülerlik kazanmıştır. SDM, doğru ve güvenilir yoğunluk ölçümleri sağlayarak modern mineral işleme tesisleri için ideal bir çözümdür.
Yoğunluk ölçümü, koyulaştırıcı verimliliğini artırmada önemli bir rol oynar ve proses kontrolü için önemli bir performans göstergesi görevi görür. Operatörler, gelişmiş ölçüm teknolojilerini ve proses kontrol stratejilerini benimseyerek koyulaştırıcı performansını optimize edebilir, geri kazanım oranlarını artırabilir ve işletme maliyetlerini düşürebilir.
Gönderim zamanı: 30 Aralık 2024